FAC FEATURED MEMBER
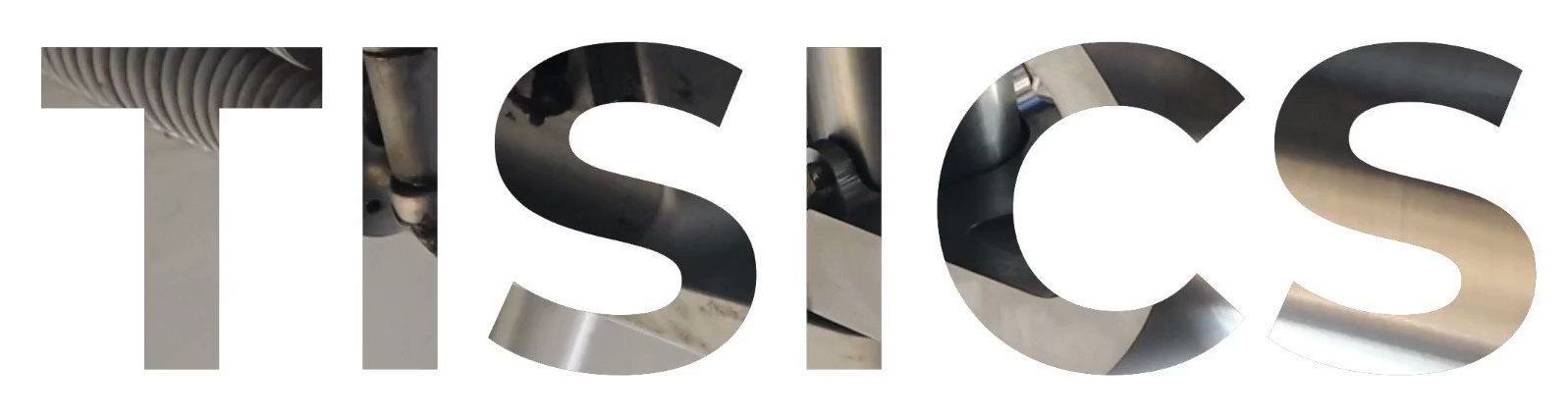
TISICS METAL COMPOSITES
TISICS specialize in the development of high-strength metal composite materials and innovative manufacturing techniques. Their core mission is to create lighter and more efficient components for various sectors, aiming for a greener future. These advanced materials offer significant weight savings and enhanced performance, allowing for optimized component design. TISICS serves industries like space, aerospace, and industrial applications, offering bespoke solutions through their integrated production capabilities based in the UK.
Business Overview
TISICS is a company pioneering lighter, faster production rate spacecraft and aircraft components using world-leading metal composite technology.
TISICS are based in the UK, specifically at 22 Invincible Road, Farnborough. Stephen Kyle-Henney is the Managing Director and founder of TISICS, having led a management buyout of the technology from QinetiQ (formerly Kinetic) in 2005 with a team of colleagues. He has a long history covering all aspects of their technology, business, and customers, starting with a student placement at BP.
Their core mission involves transforming metals for a greener, brighter future by developing high-strength metal composite and innovative net-shape technology to deliver lighter components for greener and cheaper planes, spacecraft and industrial equipment. TISICS aims to solve some of the world's toughest engineering challenges by leading a new class of materials and manufacturing technologies. They see themselves as being at the top end of materials technology, looking to make a real difference. As a nation, the UK has an ambitious target of Net Zero emissions by 2050, which will require lighter aircraft and cars, and TISICS technology aims to contribute significantly to this goal.
Products and Technology
TISICS specialises in ultra lightweight materials, making a metal composite reinforced with their own proprietary ceramic fibre. This technology takes the best of lightweight metals like aluminium and titanium, and combines them with the best ceramic, silicon carbide, to achieve more than the sum of the parts.
- They put very high strength ceramic fibres into a very high strength titanium alloy.
- Combining the two materials effectively means they can make a part half the weight of steel while being as strong as steel. This is described as "the best of both worlds" in engineering terms.
- The core benefit of their metal matrix composites is the significant weight savings, ranging from 30% to 70%. For example, doubling the stiffness of titanium means a part can be made half the weight. TISICS states their technology delivers up to 70% component weight savings.
- A notable example of their technology is a small tube that weighs about the same as a packet of crisps but is capable of carrying a 5-ton African elephant. The sources state that the UK is the only country that makes this technology.
- They also use their technology to produce net shape additive parts to reduce waste and make complex, difficult-to-machine titanium and aluminium parts. This process allows them to take small pieces of metal and bond them together into a solid with the composite integrated, keeping 95% of the material in the final component, compared to traditional manufacturing where 90% might be machined away.
- TISICS metal composites are selectively reinforced to optimise cost, performance, and mass, allowing strength to be added where it is needed.
Target Sectors and Applications
TISICS targets a range of sectors where lightweight, high-performance materials are critical:
- Space: Short lead time, fast production rate pressure vessels and spacecraft structures, as well as components for the next generation of satellites. A space tank for small satellites is mentioned as a fully qualified product they are working towards with investment.
- Aerospace: Lightweight landing gear, structural components, aero-engine component development, and actuated parts. Applying their technology to landing gear on existing aircraft fleets is seen as a potential way to save significant CO2 emissions.
- Industrial: Highly durable, corrosion-resistant structures for electrification, renewables, and potentially engine and wind components.
- Defence.
- Energy sector.
- A small amount of activity in automotive.
- Robotics.
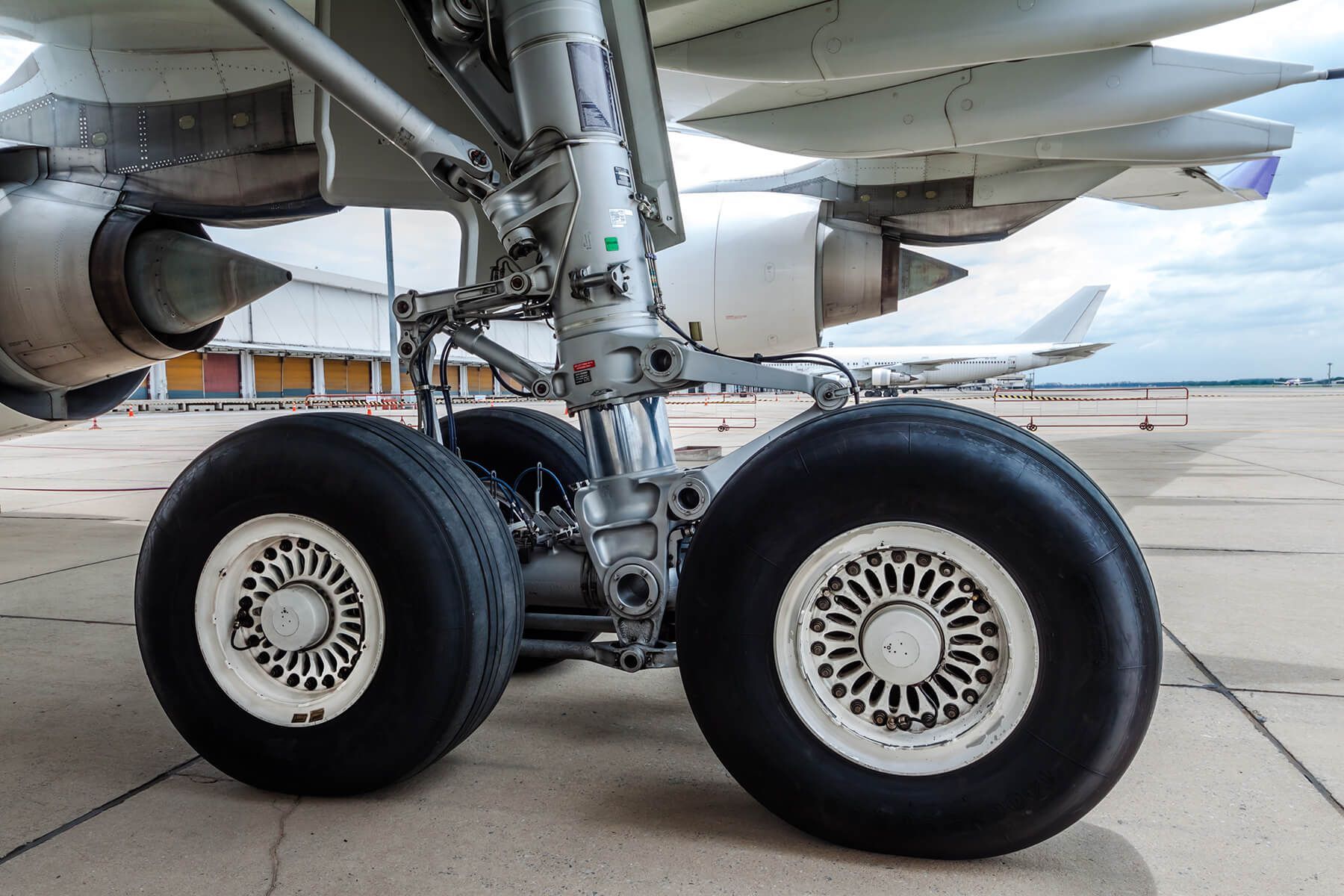
Success Stories and Achievements
TISICS has achieved significant milestones and recognition:
- Winning the Aerospace Technology & Innovation Award in 2023 for their metal composite technology. The judges saw huge potential in their submission. Winning this award was seen as "amazing" for TISICS and a "huge huge recognition" of the team's work.
- Successful demonstration of their technology through a full-size component that can be shown on aircraft. They are looking forward to seeing their technology on aircraft soon.
- Delivery of a 50% weight saving which translates directly into efficiency in the aircraft, saving fuel and CO2 emissions and contributing to making aviation Net Zero. They have achieved a phenomenal achievement by delivering this weight saving.
- Securing a project with the European Space Agency involving custom laser systems for their composite manufacturing process. This project includes developing a miniature prototype of a winding system and sophisticated monitoring using blue lasers and camera systems for precise control of composite spacing and laser bonding positioning. The prototype system is used to refine processes before scaling up to achieve multiple angles and layers.
- Receiving support from Innovate UK and the European Space Agency, which has helped them build significant technical capability and customer opportunities, especially towards meeting Net Zero emissions requirements through mass reduction.
- Being successful with the Sustainable Innovation Fund, which they state "came at the right time" and accelerated the next stage of development by four to five years. This fund allowed them to take lab-scale components to full-scale components, requiring new equipment and expertise. Winning the programme was aided by support from the KTN team, who helped refine their bid. This support allows them to introduce their technology into aircraft and vehicles sooner, starting emission savings today rather than in 10 or 20 years.
- Potential to save up to 3.7 million tons of carbon dioxide emissions a year by applying their technology to landing gear on existing aircraft fleets, which is the equivalent of the CO2 absorbed by four and a half million acres of mature forests.
- Having a small pilot facility for R&D in Farnborough with a strong team of engineers and scientists. They are developing their technology now to embed in systems by the mid-2020s.
- Identifying the need for investment now to translate current development to fully qualified products and establish a small pilot industrial facility in the Midlands.
Overall, TISICS is focused on delivering significant weight savings (30-70%) in metal components using their unique composite technology, which is key for improving efficiency and reducing emissions in sectors like aerospace and space. Their recent successes, including the Aerospace Technology & Innovation Award and projects with the European Space Agency and Innovate UK, highlight the potential and growing recognition of their technology.